SMARTer Storage
Smart Storage consists of a variety of computer-controlled systems for automatically storing and retrieving loads using stacker crane, pallet shuttle, lift, and small robots to/from defined storage locations. It is integrated with a warehouse control software (WCS), warehouse management software (WMS), or other software system.
What is SMARTer Storage?
Smart Storage ASRS (Racking, Shelf, etc.) is typically used in applications where:
- There is a very high volume of loads & SKUs being moved into and out of storage.
- Limited space but able to build upward of more than 20m to increase the storage density.
- No value is added in this process (no processing, only storage and transport).
- Accuracy is critical because of potential expensive damages to the load.
- Random and instant access to any pallet.
Uses & Application:
- Goods-to-Person for Order Picking and Packing to save time.
- Staging Orders for Shipping for a shorter preparing time.
- Managing Buffer Storage efficiently for ease of retrieval as and when is necessary.
- Storing according to the priority (FIFO), category, expiry date, etc.
a. Pallet Shuttle Racking (2-Ways & 4-Ways)
2-Ways pallet shuttle a.k.a. radio shuttle has been using in the warehouse which required high density storage at a small space to reduce land & labour costs. Pallet shuttle can be both semi and fully automated if it's integrating with Sophic&s SIM system.
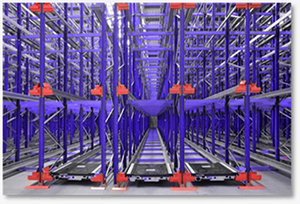
Features:
- Reach Truck is required
- Pallet space increment ~ 50%
- Can be integrated with inventory management system and ERP
Suitable for:
- High throughput of pallet goods
- High requirements for storage capacity; Up to 90% storage space
- Temporary storage of pallet goods or batch buffering of wave picking orders
- Periodic large inbound or outbound
- Required to store more pallet deeps and increasing inbound capacity
- To reduce manual operation and adopting fully automated operation
System advantages:
- High-density storage: Compared with conventional pallet racking and mobile racking, it can achieve nearly 100% aisle storage.
- Cost saving: reasonable space utilization rate reduces operating costs.
- Less damage to racking and goods: Compared to the conventional narrow aisle racking no forklift is required to drive into the racking which avoid the damage to the goods and racking.
- Expandable and improved performance: It is easy to add additional pallet shuttle to operate synchronously in order to handle more pallets.
- Comparison of Storage Space Utilization
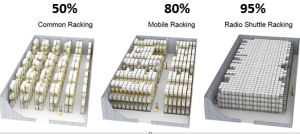
Technologies
RFID technology is used to locating, trace process, collect information, sort and pick, etc., and to write product quarantine inspection, transportation, storage, handover and other information into the coding system, and realize two-way traceability of product production, transportation, storage, handover and other information by scanning barcodes or identifying RFID information, also realize the identification of anti-counterfeiting and safety functions, ensure food safety and drug safety, and ensure the authenticity of products.
- Develops information systems by designing, developing, and installing software solutions.
- Determines operational feasibility by evaluating analysis, problem definition, requirements, solution development, and proposed solutions.
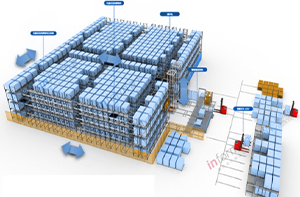
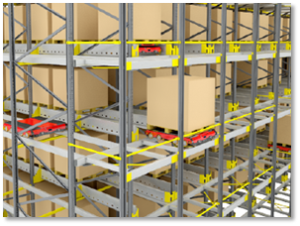
4-way radio shuttle system is a complete level of cargo location management (WMS) and equipment dispatching capability (WCS) which ensures the stable and efficient operation of the overall system.
In order to avoid waiting for the operation of radio shuttle and elevator, a buffer conveyor line is designed between elevator and rack. Pallet shuttle and elevator both transfer the pallets to the buffer conveyor line for transfer operations, thereby improving efficiency.
Four-way radio shuttle system can be well adapted to special application environments such as low warehouses and irregular shapes and can meet operating scenarios such as large changes of inbound and outbound efficiency, and high efficiency requirements. Since four-way radio shuttle system can achieve flexible project expansion and equipment increase, it can meet the demands of going online in batches and reduce customer investment pressure.
Features:
- No reach truck is required
- Lift is used to bring the pallet shuttle up & down, and move around the racking system
- Pallet space increment ~ 100%
- Can reach as high as 30m
- Integrate with inventory management system
- Load Weight: 500kg, 1000kg, 1500kg, 2000kg
- Speed: 65/85m/min (corresponding to load)
- Temperature: - 25 ~ 45°C
- Width: 1200, 1300, & 1600mm
- Length: Length 1000mm & 1200mm
System Advantages:
- Access multiple SKU's on any aisle, any level, FASTER with multiple tracks
- Shorter aisles result in better availability for pallets or pallet batches
- Allows deep-lane and shallow-lane storage formation within same racks
- Can reach beyond 12m height with vertical lift
- Highest storage density; 40% more than ASRS
- Equipped with slope climbing and automatic pallet levelling
- System configuration become standard due to features of change direction
- Standardize management process and simplify operation
- Clear visibility of inventory
- Material storage location is accurate
- All entry and exit are confirmed by scanning codes, which improves the accuracy and efficiency of operations
- Easily paired with AGV fleet, forklifts fleet or input-output conveyors
- It's scalable for any high throughput operation
- Supports automated receiving, order picking replenishment, layer picking, end-of-line production, staging for shipping
- Seamlessly pallet movement with multiple pallet shuttles
- Automatically performs inventory rotation
- Ensuring optimal performance and inventory control
- Provides full reporting on pallet traceability and SKUs stored
- Autonomous control of aging stock inventory
- Reports 100% accurate daily stock-counts
- The stock-count feature runs automatically in off-peak times
- Cross-stock check between database and pallets on storage lane for discrepancies
- WCS software is used to synchronize and manage all of Distribution Center workflows
- Storage Density Comparison
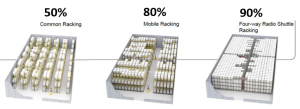
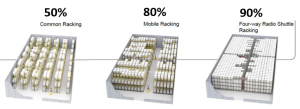
Applicable Industry
Cold chain storage (-25 degree), freezer warehouse , E-commerce , DC center , food and beverage , chemical , Pharmaceutical industry, automotive, lithium battery, Etc.
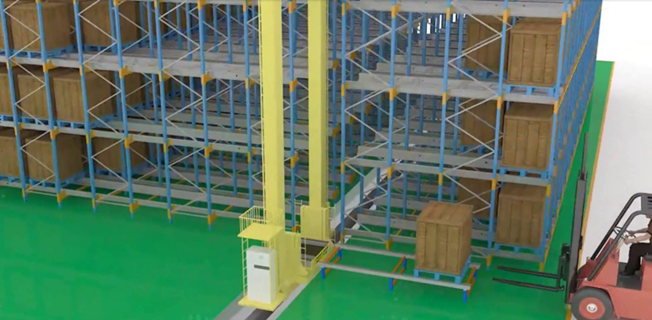
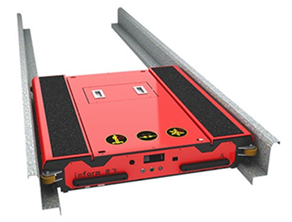
Inrover Shuttles
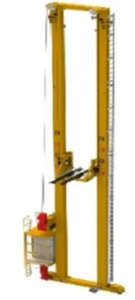
Stacker Crane
- Consists of the mature stacker crane technology & advanced functions of shuttle car
- It is completely automatic operated by WMS & WCS, and data is backed up automatically
- Uses less stack cranes by adding the aisle depth
- Low to medium SKUs and throughput
- FIFO & Random Inbound and Outbound with WMS
- For cold room with temperature -30°C to 45°C
Advantages
- Compared with AS/RS, the utilization has increased more than 30%
- Increase storage density storage 60% more than manual racking
- The cost of single storage is lower than regular AS/RS
- Flexible planning for warehouse and multi options for layout
- Improve work efficiency and reduce working time
- Saves manpower and costs
Applicable Industry:
Machinery, metallurgy, chemical, aerospace, electronics, medicine, food processing, tobacco, printing, auto parts, distribution centers, large-scale logistics supply chains, airports, ports, & military material warehouses.
In recent years, shuttle mover system has developed into a flexible, easy-to-use, energy-saving and environmentally friendly new delivery equipment in logistics industry.
In this system, the Shuttle Mover working in combination with pallet shuttle as a fully automatic and high-density storage system.
The whole system consists of Shuttle Mover, radio shuttle, racking, shuttle mover lifter, pallet conveyer system, WCS, WMS and so on.
It's widely used in different industries, such as garment, food and beverage, automobile, cold chain, tobacco, electricity and so on.
Advantages
- Highest Storage Density; Maximize space utilization
- 24 hours unmanned automatized operation
- Shuttle mover can change levels & increase flexibility
- Three independent movement directions, maximizing system efficiency
- System expandable by increasing number of INROVER Shuttle and shuttle Mover
- Adaptable to the change of season demands
- Shuttle car is charged by the shuttle mover during the movement
- Improve warehouse safety and efficiency
- Reduce warehouse operational costs
Applicable Industry:
Cold chain storage (-25 degree), Freezer warehouse, E-commerce, DC center, Food and Beverage, Chemical, Pharmaceutical industry, Automotive, Lithium battery, etc.
b. ASRS (Automated Storage & Retrieval System) - (Unit & Mini-Load)
- Fully automated storing and retrieving with inventory control
- Safe and no reach truck is required inside the racking system
- Stacker Crane is used for to storing & retrieval
- Pallet space increment up to 100% with 50m height
- Suitable for high bay warehouse
- Cold room application: -25°C ~ 45°C
- ASRS Types:
- Unit-Load AS/RS Cranes
- Fixed-Aisle
- Aisle-Changing
- High Bay
- Clad-Rack
- Mini-Load AS/RS
- Shuttle - and Bot-based AS/RS
- Carousel-based AS/RS (Vertical, Horizontal, and Robotic)
- Vertical Lift Module (VLM) AS/RS
- Micro-Load (Stocker)
System advantages:
- High space Utilization
The space utilization of AS/RS is 2-5 times than common storage. The racking can be designed as single-depth or double-depth to improve storage capacity, also compatible with any size pallet.
- Improving efficiency of storage and picking
AS/RS is dynamic storage and advanced logistics system, improving production management level. Compared with static racking system, the storage and picking efficiency is much improved.
- Labor-saving operation
The pallet moving is handled by equipment and controlled by software system. So it requires minimum labor and allows to operate unattended around the clock.
- High adaptability with other automated storage robots
AS/RS is able to work with other automated storage robots such as the shuttle car, shuttle mover, four-way shuttle and so on to meet diversified storage requirement and increase efficiency.
Benefits

Very high goods picking accuracy

Pallet throughput increase

Space saving (able to reach 50m height)

Cost saving on labour and utilities

Inventory storage density increase

Minimize pilferage of valuable goods

Maximize worker safety

Automatically performs inventory rotation

Ensuring optimal performance and inventory control

Provides full reporting on pallet traceability and SKUs stored

Autonomous control of aging stock inventory

Reports 100% accurate daily stock-counts

The stock-count feature runs automatically in off-peak times

Cross-stock check between database and pallets on storage lane for discrepancies
Functions
Automatic storing & removing of an item to/from a storage location in a predetermined location, having received an item from a processing or interface point
Maximize available space in existing structures and minimize storage space by up to 40 percent
Allows for 24 hours operation
Effective Inventory Control Management for smoother production and delivery
Specifications
Spec | Pallet shuttle |
---|---|
Load Capacity | 1000kg / pallet |
Lifting Speed | 30m / min |
Traveling Speed | 100m / min |

Phone: (604) 640 9087 / 9088 / 9089

Email: enquiry@sophicautomation.com
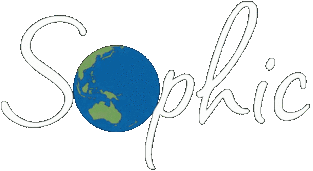
SOPHIC AUTOMATION SDN BHD
(2007010136965(794994-D))
A pure play technology company, we have delivered proven automation solutions to more than 50 MNCs & SMEs in South East Asia.
QUICK LINKS
ADDRESS
PENANG
9, 1, Jln Industri Tangkas, Taman Industri Tangkas, 14000 Bukit Mertajam Penang.
PENANG PSDC
2nd Floor, No. 1, PSDC, Jalan Sultan Azlan Shah, 11900 Bayan Lepas, Penang, Malaysia.
KUALA LUMPUR
21-13A & 21-16, Stellar Suites, Jalan Puteri 4/7, Bandar Puteri, 47100 Puchong, Selangor.
Tel: (603) 8604 7311
NEWSLETTER
©2023 Copyright Sophic Automation Sdn Bhd. All Rights Reserved | Terms of Use | Privacy | Site Map